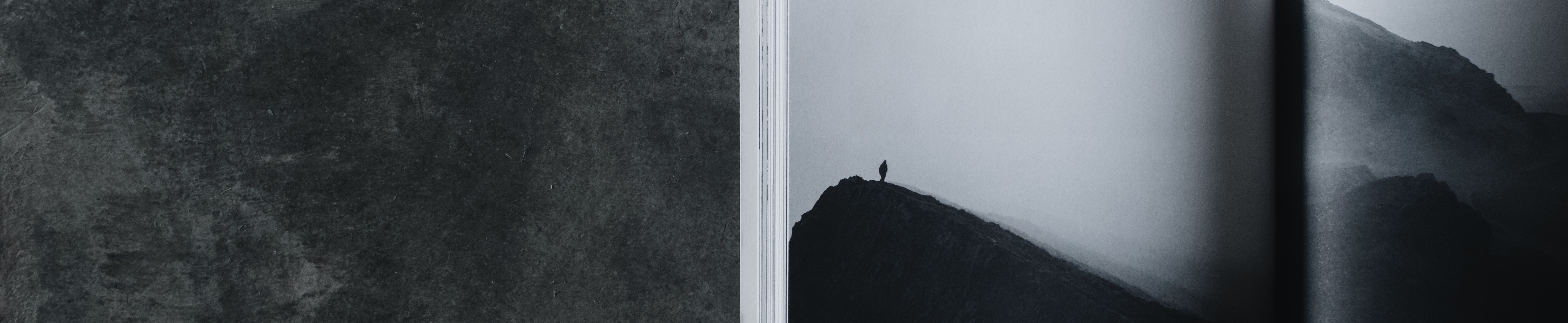
Adaptive Grippers for Grasping of Irregular Parts
Introduction
This book offers a comprehensive exploration of the state-of-the-art technologies and methodologies employed in the design and implementation of adaptive grippers. It delves into the principles of mechanics, material science, and control systems that underpin these sophisticated devices. Through a series of detailed chapters, readers will gain insights into the latest advancements, including novel mechanism, sensor integration, and adaptive control strategies that enable grippers to adjust and conform to the unique characteristics of each object.
The journey through this book is not just about understanding the technical aspects of adaptive grippers but also about appreciating the broader impact of these innovations. The ability to grasp and manipulate irregular parts with precision opens new possibilities for automation in diverse fields, from manufacturing to healthcare, and beyond. As industries continue to evolve and face new challenges, the role of adaptive grippers becomes increasingly pivotal in driving efficiency, accuracy, and versatility.
978-981-5285-58-1
Chapter 1 Introduction to Adaptive Gripping Technologies
1.1 Importance of Adaptive Grippers in Modern Automation
1.2 Evolution of Adaptive Grippers
1.3 Overview of Grasping and Manipulation Challenges
1.3.1 Single-drive adaptive grippers
1.3.2 Perception and control of clamping force
1.3.3 Intelligent grasping strategy for irregular parts
1.3.4 Flexible precision assembly technology based on manipulator
1.3.5 Existing problems and research topics
1.4 Structure and Scope of the Book
Reference
Chapter 2 Design of a Microgripper for Micro/nano Manipulation
2.1 Introduction
2.2 Mechanical Structure
2.3 Modeling And Analysis
2.3.1 Kinematics modeling
2.3.2 Static modeling
2.3.3 Dynamic Modeling
2.4 Finite Element Analysis
2.5 Experimental Tests
2.6 Conclusions
References
Chapter 3 Design of a Three-Finger Adaptive Robotic Gripper
3.1 Introduction
3.2 Mechanical System Structure
3.2.1 Motor Driver
3.2.2 Finger Structure
3.2.3 Flexible Differential Mechanism
3.3 Working Principle of Adaptive Grasping
3.3.1 Planar Analysis of Grasping Motion
3.3.2 Spatial Analysis of Grasping Motion
3.4 Flexure Hinge Design
3.4.1 Flexure Hinge Structure
3.4.2 Finite Element Simulation
3.5 Adaptive Grasping Experiments
3.6 Conclusions
References
Chapter 4 Design and Control of a Four-finger Adaptive Gripper
4.1 Introduction
4.2 Gripper design
4.2.1 Design Considerations
4.2.2 Gripper Structure
4.2.3 Working Principle
4.3 Modeling of the Gripper
4.3.1 Kinematics Analysis
4.3.2 Statics Analysis
4.4 Gripper control
4.5 Experimental Evaluations
4.5.1 Prototype Development
4.5.2 Adaptive Grasp
4.5.3 Grasping Force Control
4.5.4 Fixture to Fixture (F2F) Assembly
4.5.5 Discussions
4.6 Conclusion
References
Chapter 5 Design and Control of a Variable-Stiffness Gripper
5.1 Introduction
5.2 Development of Variable-stiffness Finger (VSF)
5.2.1 Working Principle of Stiffness Variation
5.2.2 Stiffness Modeling
5.2.3 Design of the VSF
5.3 VSF Gripper and its Characteristics
5.3.1 Prototype
5.3.2 Grasping Control & Strategy
5.3.3 Stiffness Estimation
5.3.4 Robustness & Safety Characteristics
5.3.5 Significance of Stiffness Variation
5.4 Application Experiments of The VSF Gripper
5.4.1 Adapt to Object’s Position & Shapes
5.4.2 Versatile Object Grasping
5.5 Conclusion
References
Chapter 6 Design and Control of a Dexterous Hand
6.1 Introduction
6.2 Physical Prototype
6.2.1 Mechanism Description
6.2.2 Actuator System
6.2.3 Design Features
6.3 Control Scheme
6.4 Modeling and Analysis
6.4.1 Kinematics Analysis
6.4.2 Joint Torque Computation
6.5 Conclusion
Reference
Chapter 7 Design of a Robotic Gripper for Container Twist Lock Unlocking
7.1 Introduction
7.2 Mechanism Characteristics
7.2.1 Mechanism Kinematics
7.2.2 Effects of the Design Parameters
7.3 Mechanism Optimization
7.4 Case study
7.4.1 Mechanism Simulation
7.4.2 Applied on a Robotic Gripper
7.5 Conclusion
References
Chapter 8 Assembly of T-Joint Frame Structures with a Fixturing Assistive Gripper (FAG)
8.1 Introduction
8.2 Problem description
8.3 System Overview
8.3.1 Fixturing Assistive Gripper Development
8.3.2 FFA Workcell Setup
8.4 Modeling and Algorithm development
8.4.1 2D Vision Algorithm for Pose Recognition
8.4.2 Dual Robot Cooperation
8.4.3 Robot Path Planning
8.4.4 Assembly Sequence Planning
8.5 Experiments and Verification
8.5.1 FAG Method vs Traditional Method
8.5.2 FFA Workcell Verification
8.6 Conclusion
References
Chapter 9 Full Range Gripping Force Sensing Method for Adaptive Grippers
9.1 Introduction
9.2 Full-range Gripping Force Sensing Principle
9.2.1 Gripping force sensing mechanism
9.2.2 Gripping force sensing base
9.2.3 Structural Stiffness Calculation
9.2.4 force sensing principle
9.3 Finite Element Simulation Analysis
9.3.1 Finite element analysis method
9.3.2 Relative error analysis
9.4 Experimental validation
9.4.1 Static calibration experiment
9.4.2 Analysis of relative error caused by position
9.5 Conclusion
References
Chapter 10 Grasping Detection Based on Deep Learning
10.1 Introduction
10.2 Grasp detection methods overview
10.3 Key point detection model KPDM
10.4 Pose Solving Module
10.5 Experiment
10.5.1 Data acquisition and annotation
10.5.2 Training scheme
10.5.3 Model comparison experiment
10.5.4 Grasping experiment
10.6 Conclusion
References
Chapter 11 Grasp Pose Detection Based on Regions of Interest
11.1 Introduction
11.2 YOLOv4 Object Detection Algorithm
11.3 Lightweight Rotated Object Detection Algorithm R-YOLOv4
11.3.1 Backbone Network
11.3.2 SimAM
11.3.3 ASFF Module
11.3.4 Five-Parameter Representation
11.3.5 Approximate SkewIoU Loss
11.4 Object Grasp Pose Detection
11.4.1 Five-Dimensional Grasp Rectangle
11.4.2 Principles of DeepLabV3+ Algorithm
11.4.3 Improved DeepLabV3+ Model
11.4.4 Training Loss
11.5 Experimental Results and Analysis
11.5.1 Object Detection
11.5.2 Model Parameter Analysis
11.5.3 Ablation Experiments
11.5.4 Performance Comparison
11.5.5 Image Preprocessing
11.5.6 Multi-Object Grasp Pose Estimation
11.6 Conclusion
References
Chapter 12 Original Stable Grasping Based on E-HRGrasp Detection
12.1 Introduction
12.2 Original Stable Grasping
12.3 E-HRGrasp
12.3.1 Coordinate Attention Module
12.3.2 Multi-Level Feature Aggregation Module
12.4 Experiments
12.4.1 Datasets and Experiment Setup
12.4.2 Experiments and Analysis on Custom Dataset
12.4.3 Ablation Studies
12.5 Conclusion
References
Chapter 13 Grasping Pose Estimation Based on Semantic Segmentation and Rotating Target Detection
13.1 Introduction
13.2 Description of robotic arm gripping method
13.2.1 Description of the problem
13.2.2 Detection frame mapped to gripping position in 3D space
13.3 Network Model
13.3.1 Faster-RCNN model
13.3.2 Feature Pyramid Module
13.3.3 Semantic Segmentation Module
13.3.4 R-Centernet Based Position Estimation Module
13.4 Simulation and Experimentation of Autonomous Gripping
13.4.1 Grabbing the dataset
13.4.2 Comparative Experiments on Crawl Detection Networks
13.4.3 Pose Estimation and Dynamic Simulation Experiment
13.4.4 Robot actual grasping experiment
13.5 Conclusion
References
Chapter 14 Grasping Detection Network with Uncertainty Estimation
14.1 Introduction
14.2 Related work
14.2.1 Deep Learning for Grasping Detection
14.2.2 Semi-Supervised Learning
14.2.3 Model Uncertainty Estimation
14.3 Proposed Approach
14.3.1 RGB-D Fusion Based Feature Pyramid Network
14.3.2 LocNet: Grasping Location Heatmap
14.3.3 PoseNet: Grasping Pose with Uncertainty Estimation
14.3.4 Confidence-Driven Mean Teacher
14.4 Implementation Details
14.4.1 Grasping Dataset and Preprocessing
14.4.2 Training of Grasping Detection Network
14.4.3 Semi-Supervised Domain Adaptation
14.5 Experiments and Discussions
14.5.1 Grasping Detection Network with Certainty Estimation
14.5.2 Confidence-Driven Mean Teacher Domain Adaptation
14.6 Conclusions
References
Chapter 15 Weight Imprinting Classification-Based Force Grasping with a Variable-Stiffness Robotic Gripper
15.1 Introduction
15.2 Universal Force Grasping Framework For Variable Stiffness Gripper
15.2.1 Overview of the Framework
15.2.2 Structure-Controlled Variable Stiffness Gripper
15.3 Center-Guided Weight Imprinting For Grasping Classification
15.3.1 Preliminaries and Analysis of Weight Imprinting
15.3.2 Enhancing Imprinting by Center-Guided Embedding
15.4 Vision-Based Grasping Force Sensing and Regulation
15.4.1 Visual Marks Localization and Rectification
15.4.2 Segmentation and Deflection Angle Detection
15.4.3 Stiffness Adjustment and Grasping Force Regulation
15.5 Experiments and Discussion
15.5.1 Evaluation of Imprinting Classification Performance
15.5.2 Evaluation of Force Sensing Resolution
15.5.3 Evaluation of Force Grasping Performance
15.5.4 Grasping Soft Plastic Cup of Water
15.5.5 Grasping of Various Objects
15.6 Conclusion
References
Index
Author(s) Information
CHEN Wenjie is a professor with the Anhui University and a senior member of IEEE. He received his B. Eng. degree and M. Eng. degree in mechanical engineering from Beijing University of Aeronautics and Astronautics (BUAA), China in 1985 and 1988 respectively, and his Ph.D. degree in mechatronics from Nanyang Technological University (NTU), Singapore in 1999. Prof. Chen has a more than 30 years’ experience in design and development of various industry-oriented mechanisms and systems, especially expert at applications of underactuated mechanisms to robotic assembly and handling. He led quite a number of projects relevant to manipulation and assembly under the national fundings. The design method of adaptive parallel mechanisms presented by him has led to several adaptive grippers successfully developed. Based on his research outcomes, he has published more than 100 papers in well-known journals and conferences and granted 30 patents in China and Singapore. In addition, his research efforts were also recognized by industry and academic communities. He was the consultant of several high-tech companies and government organization, as well as the committee member of several recognized international conferences. He has also been the reviewer of several famous robotics journals and governmental funding agencies. Currently, Prof Chen is leading a team conduct research of robotic flexible assembly and adaptive grasping for high-mix and low-volume industry applications.
SUN Xiantao received the B.Eng. degree in Mechanical Engineering from the University of Science and Technology Beijing, Beijing, China, in 2009, and the Ph.D. degree in Mechanical Engineering from Beihang University, Beijing, China, in 2015. Since 2019, he has been an Associate Professor with the School of Electrical Engineering and Automation, Anhui University, Hefei, China. His research interests include underactuated grippers, soft robots, variable stiffness actuators, force/torque sensors, precision manipulations, humanoid robots, and power-assisted exoskeletons, etc. To date, he has published more than 50 academic papers, obtained more than 20 authorized invention patents, and won the first prize for technological invention from the China Instrument and Control Society, as well as gold and silver medals at the Geneva International Invention Exhibition, etc.