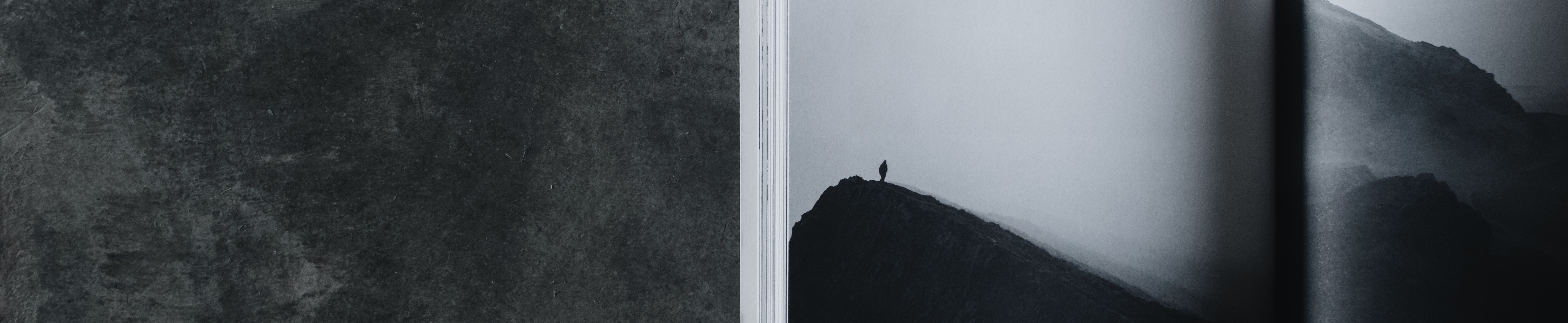
Fundamental of Glass Damage and Its Analyses Auto
Introduction
Fundamental of Glass Damage and Its Analyses Automation, edited by Hongtu He and Jiaxin Yu, is based on the latest progress of the fundamental and applications of glass damage during precision processing of related research results of the authors and others. This book systematically expounds the basic theory and application of glass damage during precision processing, and comprehensively reflects the latest research status and development trend of glass damage during precision processing.
The book is divided into 10 chapters, which consist of four parts: the basic knowledge of glass and its precision processing, the characterization of glass damage, the basic theory of glass processing damage and the intelligent detection of glass processing damage. On the basis of clarifying the basic knowledge of glass and its precision machining as well as the characterization methods, the basic theory of glass processing damage is comprehensively explained from the stress corrosion of glass surface, indentation damage of glass, scratch damage of glass, and reciprocating scratch (wear) damage of glass, and finally the application of machine vision and machine learning in the glass damage is taken as an example to illustrate its practical application in engineering.
This book can be used as a textbook for undergraduate, graduate student for mechanical engineering, materials engineering and chemical engineering, as well as a teaching reference for teachers and students of related majors in colleges and universities. It can also be used as a reference for engineers and technicians engaged in mechanical processing and manufacturing as well as glass materials.
978-981-17331-2-3
Chapter 1 Introduction
1.1 Glass history
1.1.1 History of the glass development in the world
1.1.2 History of the glass development in China
1.2 Glass classification
1.2.1 Traditional glass
1.2.2 Advanced glass
1.3 Engineering applications of glass
1.3.1 Applications in construction industry
1.3.2 Applications in transportation industry
1.3.3 Applications in photovoltaic industry
1.3.4 Applications in communication industry
1.3.5 Applications in biomedicine industry
1.3.6 Applications in high-precision fields
1.3.7 Applications in nuclear industry
1.4 Future trends
References
Chapter 2 The Fundamental of Glass
2.1 Glass melting
2.1.1 Raw materials
2.1.2 Ingredient nomenclature
2.1.3 Material calculation
2.1.4 Glass melting mechanism
2.1.5 Molten glass clarification
2.1.6 Homogenization of liquid glass
2.1.7 Special melting method
2.2 Glass structure
2.2.1 Basic chemical composition of oxide glass
2.2.2 Structural model of silicate glass
2.2.3 Structural model of borate glass
2.2.4 Structural model of phosphate glass
2.2.5 Structural models of other glasses
2.3 Density and thermal expansion
2.3.1 Introduction
2.3.2 Measurement method
2.3.3 Factors affecting glass density
2.3.4 Factors affecting thermal expansion of glass
2.4 Mechanical properties of glass
2.4.1 Elastic modulus
2.4.2 Hardness
2.4.3 Fracture strength
2.4.4 Glass strengthening
References
Chapter 3 Precision Machining of Glass and Its Damage
3.1 Cold processing of glass
3.1.1 Grinding and polishing
3.1.2 Engraving
3.1.3 Spray flowers
3.1.4 Etching
3.1.5 Glass cleaning
3.2 Thermal processing of glass
3.2.1 Tempering
3.2.2 Hot-bent and hot-melt glass
3.2.3 Stained glazed glass
3.3 Special processing methods
3.3.1 Micro-milling of glass
3.3.2 Electrochemical processing of glass
3.3.3 Nanoimprint
3.3.4 Glass 3D printing
Reference
Chapter 4 Characterization of Glass Structure, Properties, and Damage
4.1 Mechanical property
4.1.1 Universal material testing machine
4.1.2 Universal hardness tester
4.1.3 Nanoindenter
4.1.4 Fatigue testing machine
4.1.5 Multifunctional friction and wear testing machine
4.2 Topography analysis
4.2.1 Mechanical stylus profiler
4.2.2 Optical profiler
4.2.3 Optical probe profiling
4.2.4 Scanning Electron Microscope
4.2.5 Scanning Tunneling Microscope
4.2.6 Atomic Force Microscope
4.3 Compositional analysis
4.3.1 X-ray photoelectron spectroscopy
4.3.2 Infrared Spectroscopy
4.3.3 Raman spectroscopy
4.3.4 Nuclear Magnetic Resonance Spectroscopy
4.3.5 Other analyses
4.4 Optical analysis
4.4.1 Radiographic inspection technology
4.4.2 Ultrasonic testing technology
4.4.3 Penetration detection technology
4.4.4 Other detection techniques
4.5 Molecular dynamics simulation
4.5.1 System establishment
4.5.2 Establishment of potential functions and system parameters
4.5.3 Results analysis methods
References
Chapter 5 Stress-corrosion of glass
5.1 Fracture toughness
5.2 Material fracture in a non-corrosive environment
5.3 Stress corrosion cracking of silicate glass
5.3.1 Zone 0: Environmental Limit
5.3.2 Zone I
5.3.3 Zone II
5.3.4 Zone III
5.4 Stress corrosion cracking behavior of sodium borosilicate glass
5.4.1 Relationship between glass composition and Ke in region 0
5.4.2 Relationship between v and KI and glass composition in region I
References
Chapter 6 Indentation damage of Glass
6.1 Indentation instruments
6.1.1 Indentation principle
6.1.2 Measuring range and classification
6.2 Shape and selection of the indenter tip
6.2.1 Shape of indenter tip
6.2.2 Selection of indenter tip
6.2.3 Effect of indenter tip passivation
6.3 Factors affecting indentation behaviors
6.3.1 Effect of indentation load
6.3.2 Effect of holding time
6.3.3 Effect of loading rate
6.4 Effect of material property
6.4.1 Effect of glass composition
6.4.2 Effect of Poisson’s ratio
6.4.3 Effect of glass history
6.4.4 Effect of water content
6.5 Effect of ambient conditions
6.5.1 Effect of temperature
6.5.2 Effect of humidity
6.5.3 Effect of radiation
6.6 Prevention of indentation damage
6.6.1 Thermal tempering
6.6.2 Chemical tempering
6.6.3 Coating
6.6.4 Etching
References
Chapter 7 Scratch damage on glass surfaces
7.1 Background of scratch test
7.1.1 Historical study of scratch tests
7.1.2 Method and principle of scratch tests
7.2 Factors affecting scratch behaviors
7.2.1 Effect of scratch load
7.2.2 Effect of scratch speed
7.2.3 Effect of scratch tip property
7.2.4 Effect of ambient environments
7.2.5 Effect of glass composition
7.3 Prevention of scratch damage
7.3.1 Thermal treatment
7.3.2 Coating
7.3.3 Etching
7.3.4 Chemical strengthening
References
Chapter 8 Wear damage on glass surfaces
8.1 Macro- and micro-wear
8.1.1 Basic definition
8.1.2 Research methods
8.2 Effect of normal load
8.2.1 Silicate glass
8.2.2 Phosphate glass
8.3 Effect of counter-surface
8.3.1 Silicate glass
8.3.2 Phosphate glass
8.4 Effect of ambient environments
8.4.1 Silicate glass
8.4.2 Phosphate glass
8.5 Effect of speed
8.5.1 Silicate glass
8.5.2 Phosphate glass
8.6 Prevention of wear damage
References
Chapter 9 Application of machine vision in glass defect characterization
9.1 Introduction
9.2 Research background
9.2.1 Glass processing defects
9.2.2 Research advances of glass defect detection technology
9.2.3 Overview of machine vision technology
9.3 Basic principles and system of defect detection
9.3.1 Basic principles of defect detection
9.3.2 Defect detection system
9.4 Research status of defect detection
9.4.1 Surface particles and scratches
9.4.2 Internal defects
9.4.3 Corner quality
9.5 Main problems and future trends of glass defect detection
9.5.1 Main problem with glass defect detection systems
9.5.2 Future trend of glass defect detection systems
References
Chapter 10 Predictions of glass properties by machine learning
10.1 Prediction methods of ML
10.1.1 Data consolidation and cleansing
10.1.2 Introduction of ML methods
10.2 Prediction of glass performance by ML
10.2.1 Elastic modulus of glass
10.2.2 Glass transition temperature
10.2.3 Glass corrosion resistance
10.2.4 Wear resistance of glass
10.2.5 Glass product defects
10.3 Future trends
References
Author(s) Information
Hongtu He, Male, Ph.D., Associate Professor, visiting scholar at Pennsylvania State University (2012-2014 and 2018-2020), Sichuan Province Academic and Technical Leader Reserve Candidate (2022), Membership of American Ceramic Society, American Chemical Society, American Society of Tribology and Lubrication Engineers, Singapore Viser Mechanical Engineering Committee, and the young editorial board member of the academic journals such as International Journal of Minerals, Metallurgy and Materials (IF=3.85), Journal of Materials Engineering (EI journal), and Journal of Aeronautical Materials. His main research interests include glass surfaces, micro-tribology, energetic materials, and machine learning. He has hosted several projects such as the National Natural Science Foundation of China, published more than 60 academic papers such as in Acta Mater. and Tribol. Int., and applied for over 10 invention patents. He won the second prize of Sichuan Province Science and Technology Progress Award.
Jiaxin Yu, Male, Ph.D., Professor, the Dean of the School of Manufacturing Science and Engineering, Southwest University of Science and Technology. He is National Young talented scholar, visiting scholar at Yale University, high-level talent expert in Sichuan Province, the 15th Mianyang Top Ten Outstanding Youths, the executive deputy director of the Key Laboratory of Manufacturing Process Testing Technology of the Ministry of Education, the director of the Tribology Branch of the Chinese Mechanical Engineering Society, the vice chairman of the Tribology Special Committee of the Sichuan Mechanical Engineering Society, and the young editorial board member of the academic journal Surface Technology (EI Journal). His research interests include tribology, surface and interfaces, ultra-precision machining. He has hosted over more than 30 projects including 3 projects from National Natural Science Foundation of China, and published more than 80 papers in Commun. Mater, ACS Appl. Mater. & Inter., J. Mater. Sci. Tech., Friction, Appl. Phys. Lett. and other journals; He has applied for more than 20 national invention patents; He won the second prize of Sichuan Province Science and Technology Progress Award (ranked 1st) and the second prize of Sichuan Province Teaching Achievement Award (ranked 3rd).